Mantenimiento correctivo: Qué es, tipos y cómo aplicarlo
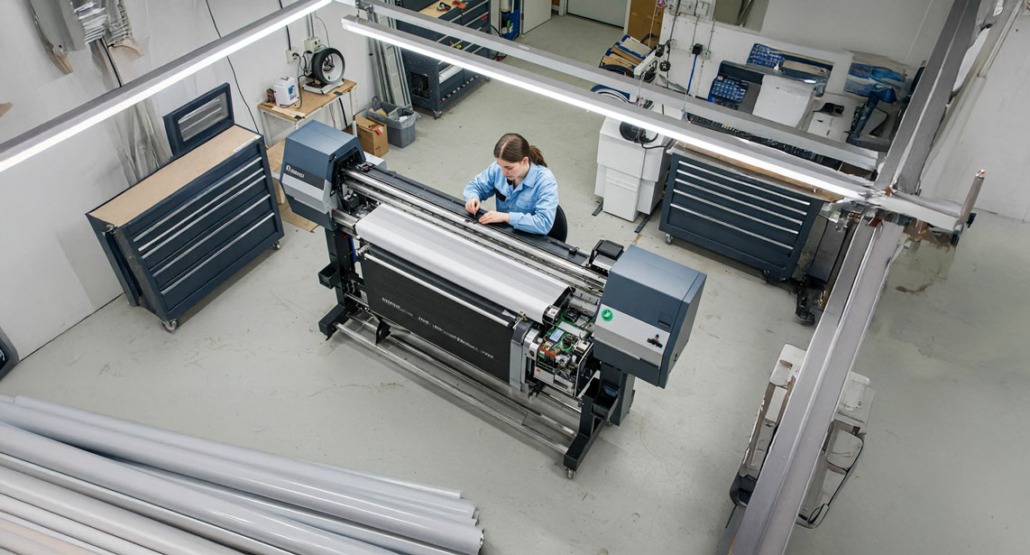
Si trabajas con maquinaria y equipamiento seguramente habrás vivido esta escena: plena jornada laboral, la producción a toda máquina y, de repente, el silencio. Una pieza clave se detiene, una fuga aparece, un sistema crítico deja de responder. En esos momentos de tensión, donde cada minuto de inactividad se traduce en costes y riesgos, entra en escena una de las modalidades de mantenimiento más fundamentales, aunque a menudo malentendida: el mantenimiento correctivo.
Pero,¿qué es exactamente? ¿Es simplemente «apagar fuegos»? ¿O tiene un lugar estratégico dentro de un plan de gestión de activos moderno? A menudo se le contrapone al mantenimiento preventivo, la estrategia proactiva de evitar fallos. Sin embargo, comprender a fondo este tipo de mantenimiento consus diferentes facetas, sus pros y contras, y cuándo aplicarlo de forma inteligente; es esencial para cualquier profesional o estudiante del sector.
En este artículo exploraremos el concepto, desmitificando su rol y proporcionando las claves para gestionarlo eficazmente.
¿Qué es el mantenimiento correctivo?
Es el conjunto de tareas técnicas destinadas a reparar o corregir fallos, averías o funcionamientos defectuosos una vez que estos ya se han manifestado en un equipo, activo o sistema.
A diferencia del mantenimiento preventivo, que busca anticiparse a los fallos mediante inspecciones y sustituciones programadas, el mantenimiento correctivo opera bajo una lógica reactiva. No sigue un calendario preestablecido (salvo en su variante planificada, que veremos más adelante), sino que se activa en respuesta a una necesidad concreta: algo se ha roto o no funciona como debería, y hay que arreglarlo para restaurar su funcionalidad y fiabilidad operativa. Su objetivo principal es devolver el activo a su estado operativo normal lo más rápido y eficientemente posible, minimizando el impacto negativo.
¿Cuándo entra en juego el mantenimiento correctivo?
La necesidad de aplicarlo puede surgir en una variedad de situaciones. No se limita únicamente a la parada total de una máquina. Algunos de los disparadores más comunes incluyen:
Fallo completo del equipo
La situación más obvia. Una máquina deja de funcionar por completo (un motor gripado, un sistema informático que no arranca).
Mal funcionamiento / funcionamiento incorrecto
El equipo opera, pero no según sus especificaciones (una bomba que no da la presión adecuada, un sensor que da lecturas erráticas, una máquina que produce piezas defectuosas).
Degradación del rendimiento
A veces, la máquina no se para de golpe, pero te empieza a ‘hablar’: ese ruidito nuevo que antes no hacía, esa vibración que te mueve los papeles de la mesa, la factura de la luz que se dispara o esa tarea que antes hacía en 5 minutos y ahora tarda 10. Son señales de alerta que, si no se corrigen, pueden llevar a un fallo mayor.
Preocupaciones de seguridad
Cualquier condición que represente un riesgo para el personal, las instalaciones o el medio ambiente (una fuga de producto químico, un cableado eléctrico dañado, un sistema de seguridad que no responde). Estas situaciones suelen requerir una intervención correctiva emergente.
Tiempo de inactividad no planificado
Cualquier interrupción inesperada de las operaciones causada por un problema en un activo.
Averías durante el mantenimiento preventivo
Irónicamente, a veces durante una inspección o tarea preventiva se descubre un fallo oculto o incipiente que requiere una acción correctiva inmediata o planificada.
Informes de operarios o usuarios
El personal que trabaja directamente con los equipos a menudo detecta anomalías o problemas antes que nadie, generando la necesidad de una intervención correctiva.
Tipos de mantenimiento correctivo: No toda reacción es igual
Mantenimiento correctivo no planificado (o Emergente / Contingente / Reactivo)
Esta es la forma más pura de reacción. Se actúa inmediatamente después de que ocurra un fallo inesperado y crítico que requiere atención urgente para restaurar la operación o la seguridad.
Se caracteriza por ser imprevisto, forzado y de una alta urgencia. El objetivo principal es minimizar el tiempo de parada a toda costa.
Este tipo de mantenimiento suele ser el más costoso por sus horas extras, la necesidad de enviar de forma urgente algunas piezas, el estrés que genera en el entorno laboral, además es propenso a soluciones temporales («parches») porque cuando todo es para ayer, prepárate para: pagar horas extra como si no hubiera un mañana, rezar para que esa pieza llegue en un envío urgente de corta duración y cruzar los dedos para que el ‘apaño’ rápido que has hecho aguante lo necesario.
Mantenimiento correctivo planificado (o programado / diferido)
Este ocurre cuando se detecta un fallo o una condición de degradación que aún no ha causado una parada crítica o un riesgo inmediato, pero que se sabe que empeorará. Permite planificar la intervención para un momento más oportuno (ej. parada programada de planta, fin de semana, periodo de baja producción).
Entre sus características están:
- Permite cierta planificación (recursos, piezas, personal)
- Reduce la urgencia y el caos
- Suele permitir una reparación más completa y duradera
- Se basa en la detección temprana (monitorización, inspecciones).
Se le puede aplicar una estrategia de variante diferido, es decir se puede tomar la decisión de posponer una reparación necesaria pero no urgente hasta un momento conveniente, evaluando que el riesgo de esperar es aceptable.
Otras Clasificaciones (según la naturaleza o urgencia de la tarea)
A veces, se usan términos adicionales para describir la intervención correctiva:
- Reparación: Arreglar una avería específica para restaurar la función.
- Reconstrucción: Desmontaje significativo para reemplazar o reparar componentes mayores y devolver el equipo a un estado óptimo.
- Normal: Reparación de equipos no esenciales cuya falla no impacta directamente seguridad o producción. Permite mayor flexibilidad en la programación.
- Emergente: Intervención inmediata requerida por un riesgo inminente para la seguridad de personas o instalaciones.
- Crítico: Intervención urgente por la importancia del fallo en el proceso productivo o funcional.
- Urgente: Requiere celeridad para evitar paradas significativas, aunque sea menos grave que el crítico o emergente.
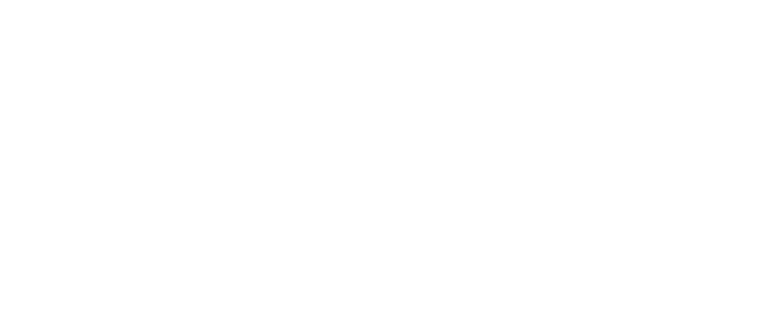
El proceso típico del mantenimiento correctivo
Aunque el flujo de trabajo para atender una acción correctiva en una empresa puede variar según la urgencia y complejidad, la intervención en un trabajo correctivo suele seguir los siguientes pasos:
- Detección del fallo: Identificación de la anomalía (por un operario, un sensor, una inspección).
- Notificación / Solicitud: Creación de un aviso/incidencia o una orden de trabajo (OT) describiendo el problema.
- Diagnóstico: Investigación por parte del personal técnico para identificar la causa raíz del fallo y determinar la solución.
- Planificación (si aplica): Si es Mantenimiento Correctivo Planificado, se programan los recursos: técnicos necesarios, repuestos, herramientas, permisos de trabajo, coordinación con operaciones para la parada del equipo. Para el No Planificado, esta fase es más reactiva y centrada en conseguir lo necesario urgentemente.
- Ejecución: Realización de la reparación, sustitución de piezas o ajuste necesario.
- Pruebas y verificación: Comprobación de que el equipo vuelve a funcionar correctamente según sus especificaciones.
- Puesta en marcha: Devolución del activo al servicio operativo.
- Documentación: Una vez que todo vuelve a la normalidad, toca el momento menos glamuroso pero súper importante: documentarlo todo. Registro de la OT completada, detallando el trabajo realizado, tiempo empleado, piezas usadas y costes. Esta información es vital para el historial del activo y análisis futuros.
Ventajas del mantenimiento correctivo
Aunque a menudo se le ve negativamente, el mantenimiento correctivo, especialmente cuando se aplica estratégicamente, también ofrece ventajas:
La primera, es el Menor coste planificado (A corto plazo). Al no requerir invertir en planificación, programación y ejecución de tareas preventivas si el fallo no ocurre no existe gasto. Para activos de baja criticidad y bajo coste de fallo, puede ser económicamente viable si los fallos son infrecuentes.
Otra ventaja que ofrece es que la planificación inicial es mínima. No se invierten recursos en planificar tareas que quizás nunca sean necesarias. La acción se desencadena por la incidencia. Además, la Simplicidad conceptual también es una ventaja: si algo se rompe, se arregla.
También hay que destacar la Eficiencia en la asignación de recursos. Es decir, los recursos (técnicos, piezas) se movilizan solo cuando hay una necesidad confirmada, evitando gastar en prevención «por si acaso» en activos donde no compensa.
Por último, este tipo de mantenimiento ofrece Flexibilidad y adaptabilidad permitiendo responder a eventos imprevistos que las estrategias preventivas no siempre pueden prever. Cada fallo es una fuente de datos y Analizar por qué falló (Análisis Causa Raíz – RCA) puede llevar a mejoras en el diseño, la operación o incluso en el plan de mantenimiento preventivo de equipos similares siendo cada suceso una oportunidad de aprendizaje constante.
Es crucial entender que muchas de estas ventajas son relativas o dependen fuertemente del contexto (criticidad del activo, coste y frecuencia de fallos).
Desventajas del mantenimiento correctivo
Confiar exclusiva o excesivamente en el mantenimiento correctivo conlleva riesgos y desventajas que suelen superar sus beneficios, especialmente para activos importantes:
Los fallos ocurren sin aviso, dificultando enormemente la planificación de la producción, los recursos de mantenimiento y los presupuestos. Genera un ambiente de trabajo reactivo y estresante.
Al momento de tener un paro completo de una maquinaria, El tiempo total de parada suele ser mayor que en una intervención planificada. Incluye el tiempo hasta la detección, diagnóstico, espera de repuestos, movilización de técnicos y la reparación en sí, a menudo bajo presión.
Aunque te ahorres la planificación del preventivo, los costes totales son más elevados. Cuando una máquina importante falla de verdad, los costes suelen dispararse a causa de:
- Costes directos: Reparaciones urgentes, tarifas de horas extra, envío exprés de repuestos.
- Costes indirectos: Pérdida de producción (lucro cesante), penalizaciones por retrasos, posible daño a la reputación, costes por impacto en calidad.
- Daños colaterales: Un fallo puede causar daños en otros componentes o sistemas cercanos.
Los fallos inesperados pueden crear mayores riesgos de seguridad. Las reparaciones realizadas con urgencia y bajo presión aumentan la probabilidad de errores humanos o soluciones incompletas que comprometan la seguridad futura.
El mantenimiento reactivo reduce la vida útil de los activos. Permitir que los equipos funcionen hasta fallar acelera su degradación general. Los fallos recurrentes pueden causar un desgaste que acorta significativamente la vida útil esperada del activo.
La necesidad urgente de una pieza específica trae problemas con repuestos tales, como: productos fuera de stock, descatalogados o con largos plazos de entrega, prolongando aún más la parada.
Además, el impacto negativo puede llegar a influir en clientes y operaciones, ocasionados por los retrasos en entregas, inconsistencias en calidad y paradas de servicio que afectan directamente la satisfacción del cliente y la eficiencia operativa global.
Finalmente, fomenta una mentalidad de «apagar fuegos» en lugar de una cultura proactiva de prevención, fiabilidad y mejora continua.
La decisión estratégica: ¿Cuándo es aceptable el mantenimiento correctivo?
Viendo las desventajas que tiene, podrías pensar: ‘¡Entonces el correctivo tengo que evitarlo!’. Pues no, tampoco es eso. Sería genial vivir en un mundo sin averías, pero no es realista. La clave no es eliminarlo, sino ser inteligente y decidir cuándo y dónde podemos permitírnoslo sin que nos explote en la cara. Y eso, depende de lo crítico que sea el activo y de cuánto te duela (en tiempo y dinero) si se para. La clave está en la estrategia y la criticidad del activo.
En equipos no críticos cuya falla tiene un impacto mínimo o nulo en la seguridad, el medio ambiente, la producción principal o los costes operativos totales (una bombilla en un pasillo, un ventilador auxiliar no esencial), este mantenimiento puede ser implantado como una estrategia predominante.
En activos donde el coste combinado de la reparación (piezas + mano de obra) y el tiempo de inactividad asociado es muy bajo, también puede ser aceptable. Incluso en equipos que son baratos, fáciles de reemplazar o de rápida reparación por tener componentes modulares.
Por otro lado, existen casos extraordinarios en el que no existen tareas preventivas efectivas imposibilitando el mantenimiento preventivo o que el coste de realizarlas sea prohibitivamente alto en comparación con el riesgo de fallo. En estas situaciones el mantenimiento correctivo es la única opción
Si existe un sistema de respaldo (Activos redundantes) que se activa automáticamente en caso de fallo del primario, la urgencia de la reparación correctiva disminuye, aunque sigue siendo necesaria eventualmente. En esta situación la viabilidad de implantarlo también crece.
En conclusión, la decisión de aplicar una estrategia predominantemente correctiva (a veces llamada «Run-to-Failure» o «Correr hasta Fallar») debe basarse en un análisis de criticidad riguroso. Este análisis evalúa la probabilidad y las consecuencias del fallo de cada activo para determinar su importancia estratégica. Depender del mantenimiento correctivo para activos críticos es, casi universalmente, una mala práctica de gestión.
El mantenimiento correctivo dentro de una estrategia integral
En la práctica moderna, el mantenimiento correctivo (CM) no opera en el vacío. Es una pieza más dentro de un ecosistema que busca el equilibrio óptimo entre reactividad y proactividad.
Relación con mantenimiento preventivo (PM)
El PM busca reducir la necesidad de CM para activos importantes. Sin embargo, los datos generados por las intervenciones correctivas (qué falló, por qué, cuánto tardó en repararse) son información valiosísima para ajustar y optimizar el plan de PM (cambiar frecuencias, añadir tareas, revisar procedimientos). El Análisis Causa Raíz (RCA) de los fallos correctivos es fundamental para esta retroalimentación.
Relación con mantenimiento predictivo (PdM)
Las técnicas predictivas (análisis de vibraciones, termografía, análisis de aceites, ultrasonidos, etc.) detectan condiciones anómalas antes de que causen un fallo funcional. Esto permite convertir lo que habría sido un Trabajo Correctivo No Planificado en uno Planificado, realizando la reparación necesaria de forma controlada y programada, con todas las ventajas que ello implica.
Una estrategia de mantenimiento madura utiliza una combinación de estas técnicas, aplicando el enfoque más adecuado a cada activo en función de su criticidad, modo de fallo, coste y riesgo asociado.
El rol del software GMAO en la gestión del correctivo
Aunque el mantenimiento correctivo sea reactivo, su gestión puede (y debe) ser eficiente. Aquí es donde un software de Gestión de Mantenimiento Asistido por Ordenador (GMAO o CMMS) juega un papel crucial, ofreciendo:
- Gestión centralizada de órdenes de trabajo: Permite crear, asignar, priorizar y seguir el progreso de las OTs correctivas de forma rápida y transparente.
- Acceso rápido a información del activo: Los técnicos pueden consultar el historial de mantenimiento, manuales, diagramas y especificaciones directamente desde el sistema (a menudo vía móvil), agilizando el diagnóstico.
- Gestión de repuestos: Ayuda a verificar la disponibilidad de piezas necesarias y a gestionar su consumo, reduciendo las esperas.
- Documentación y análisis: Registra todos los detalles de la intervención, creando un historial valioso para análisis futuros (identificar fallos recurrentes, calcular MTTR(Tiempo Medio Para Reparar)).
- Comunicación y Colaboración: Facilita la comunicación entre operaciones (quien reporta el fallo) y mantenimiento (quien lo repara).
- Priorización: Ayuda a gestionar y priorizar múltiples solicitudes correctivas basándose en la criticidad del activo o la urgencia definida.
Un GMAO no elimina la naturaleza reactiva del correctivo, pero sí aporta orden, eficiencia y visibilidad a su gestión.
Mejores prácticas para gestionar el mantenimiento correctivo
Para minimizar los impactos negativos ocasionados por las averías, considera estas buenas prácticas:
- Priorización clara: Establece un sistema para priorizar las reparaciones correctivas basado en la criticidad del activo y el impacto del fallo (seguridad primero, luego producción crítica, etc.).
- Proceso ágil de reporte y documentación: Facilita que los operarios reporten fallos rápidamente. Documenta cada intervención de forma completa.
- Gestión eficiente de órdenes de trabajo: Utiliza un GMAO para gestionar el flujo de trabajo.
- Equipo técnico capacitado: Asegúrate de que los técnicos tengan las habilidades y herramientas adecuadas para diagnosticar y reparar eficazmente.
- Gestión estratégica de repuestos: Mantén un inventario optimizado de las piezas críticas o de alta rotación para las reparaciones correctivas más probables o importantes.
- Análisis causa raíz (RCA): No te limites a reparar. Investiga por qué falló el activo, especialmente en fallos críticos o recurrentes, para implementar acciones que eviten su repetición.
- Cultura de mejora continua: Utiliza los datos de las intervenciones correctivas para aprender y mejorar continuamente tanto los procesos de reparación como las estrategias preventivas/predictivas.
- Comunicación fluida: Fomenta la colaboración entre Mantenimiento, Operaciones e Ingeniería.
Mantenimiento correctivo: necesario, pero no suficiente
El mantenimiento correctivo es la respuesta esencial ante lo inesperado, la acción necesaria para devolver la vida a un activo que ha fallado. Ignorar su existencia o su necesidad es imposible en cualquier entorno operativo real. Ofrece flexibilidad y, en contextos muy específicos de baja criticidad, puede ser una opción económicamente viable a corto plazo.
Sin embargo, la dependencia exclusiva del mantenimiento correctivo es una estrategia reactiva, costosa y arriesgada para la mayoría de los activos importantes. La imprevisibilidad, el aumento del tiempo de inactividad, los costes ocultos, los riesgos para la seguridad y la reducción de la vida útil de los equipos son desventajas demasiado significativas como para ignorarlas. La gestión moderna y eficaz del mantenimiento reside en el equilibrio estratégico. El mantenimiento correctivo siempre tendrá su lugar para atender fallos imprevistos o para activos donde el riesgo no justifica la prevención. Pero debe gestionarse eficientemente (apoyado por herramientas como el GMAO y buenas prácticas) e integrarse dentro de un marco más amplio que priorice la proactividad a través del mantenimiento preventivo y predictivo, guiado siempre por un análisis riguroso de la criticidad de los activos. Solo así se puede aspirar a la máxima fiabilidad, seguridad y rentabilidad operativa.